Basic knowledge of double sided tape
xinstDec 29, 2020
Double sided Adhesive tape has been around for nearly 100 years, bringing great convenience and efficiency to mankind. The reason why tape can stick is that it is coated with a layer of adhesive to make the tape stick to the object. The earliest adhesive comes from animals and plants. In the nineteenth century, rubber was the main component of the adhesive; but it is widely used in modern times. Various polymers.
According to its efficacy, it can be divided into: high temperature tape, double sided tape, insulating tape, special tape, pressure sensitive tape, die cut tape. Different functions are suitable for different industry needs, and they are necessary for various industries.
Definition of tape
Through touch and light pressure, the tape can be easily bonded to the surface of the adherend. Adhesive tape is a viscoelastic polymer with both liquid and solid properties. Therefore, compared with glue, the adhesive tape does not require a curing process during bonding, which can save man-hours. Tapes are used in a wide range of applications. In addition to daily office tape products, tapes also have many applications in industrial fields such as automobiles, electronics, paper printing, construction, home appliances, new energy, and rail transit.
The structure of the tape
Tapes generally consist of coatings with various functions. The adhesive is coated on one or both sides of the substrate (to make single-sided or double-sided tape). Adhesive tape can be divided into three basic categories according to the structure:
(1) Single-sided tape (Single-sided Tape), that is, only one side is coated with an adhesive layer.
(2) Double-sided tape (Double-sided Tape), that is, adhesive tape coated on both sides.
(3) Transfer tape, that is, a tape without a substrate, which consists of only release paper coated with adhesive directly.
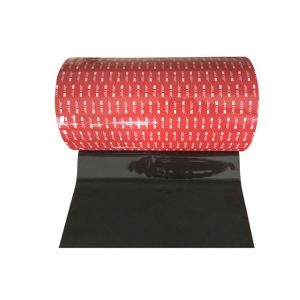
Surface treatment of double-sided tape
The bonding surface must be clean, dry, smooth, free of rust and oil stains. Avoid finger contact with the rubber surface during operation, and press hard after pasting to ensure full contact of the rubber surface.
① Perform proper sanding first. It is recommended to use 3M company cleaning flannel to remove rust and increase the micro contact area to improve the bonding effect.
② For general surfaces, it is recommended to use a mixture of isopropyl alcohol alcohol (IPA) and water (mixing ratio is 1:1) to clean oil and dust.
③ Use a clean cloth or paper towel to clean and dry the bonding surface.
④ For some surfaces with large roughness, many meshes, extremely easy to wet (such as glass), and chemical reactions (such as brass), pretreatment is required. It is recommended to use primer.
Various characteristics and advantages of the substrate
The task of the substrate is to fix the adhesive and primer. The substrate material is very rich, from paper to plastic film, etc., different materials have different characteristics and are suitable for various application scenarios.
Film: tear-proof
The film can be used to make particularly thin anti-tear tape. However, the difference when different films are used as tape substrates is also very large. It depends on the raw material of the substrate: whether it is polyvinyl chloride (PVC), polyethylene (PE), polypropylene (PP), polyethylene terephthalate (PET) or other raw materials.
For example: PVC can be very flexible, so it is mainly used to make insulating tape and masking tape, such as the tape used in the plastering process. Very soft PVC can be used to insulate the sheath of the wire. In contrast, hard PVC can maintain a stable shape, so it is suitable for the production of packaging tape and inner packaging. All PVC films have a common feature: very durable and not easy to ignite. They can be printed and embossed.
PE or PP film is mainly used as the base material of office tape. They can also be used as surface protection and packaging materials (packaging).
PET film has very unique characteristics. They are mainly used as the substrate between two primers in double-sided tapes. Due to its thermal conductivity, it is also suitable for the task of thermal management in electronic equipment. Their UV stability is excellent, so they are often used in outdoor environments.
In addition to the uses mentioned above, polyurethane, polyimide, and cellophane/cellulose acetate are also used as film substrates because of their flexibility, water resistance and high temperature resistance.